No matter how smoothly a business operates, there is always potential for improvement. Processes are established to ensure continuity, yet these can become outdated over time, leading to project delays and increased costs.
Continual process improvement offers a structured approach for organizations to eliminate inefficiencies and constantly seek enhancement.
The success of business process transformation depends on the right mindset, culture, and capabilities and requires appropriate methodologies and tools to drive and sustain improvements.
Process improvement methodologies serve as a robust foundation for continuous business agility. Without a set of shared practices to navigate improvement efforts, organizations will likely resort to improvisation, a strategy that undermines long-term success.
This article will guide you in creating a process improvement strategy by explaining what process improvement methodologies entail and their significance while exploring the 18 most renowned methodologies.
What are Process Improvement Methodologies?
Process improvement methodologies provide a structured way to assess and refine existing operations. Their primary aim is to enhance efficiency, adapt processes to emerging business requirements, and optimize workflows, thereby reducing expenditures and boosting profits.
Instead of making arbitrary adjustments to business operations, these methodologies enable organizations to identify areas for enhancement, apply modifications, and evaluate the impact of these changes compared to prior performance.
This methodological approach relies on quantitative data to discern the effectiveness of implemented changes, offering clear insights into successes and shortcomings. Such methodologies facilitate monitoring these adjustments, paving the path for further improvements.
The Importance of Process Improvement Methodologies
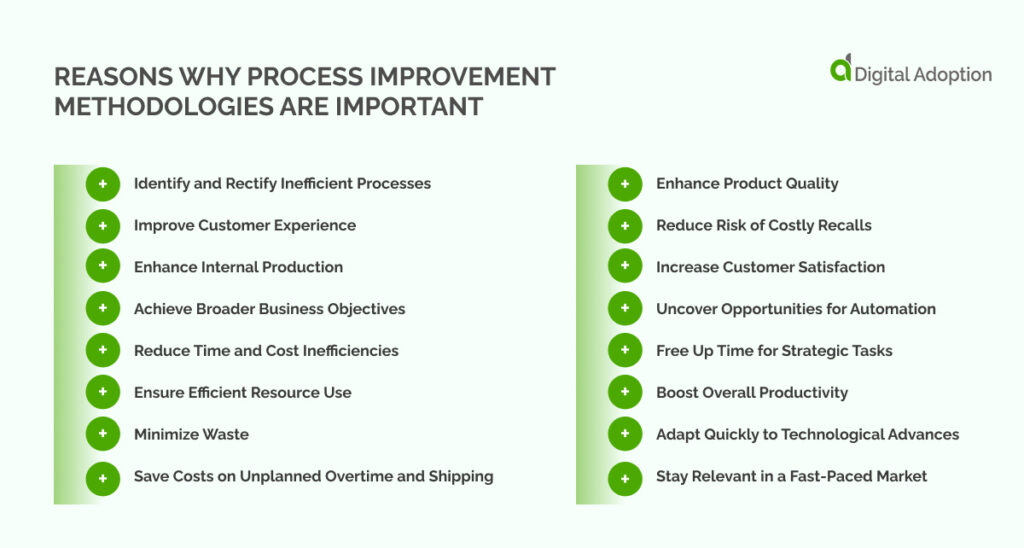
Process improvement methodologies are crucial in enhancing business operations for several vital reasons. They help identify and rectify inefficient processes that can lead to defective work, negatively impacting customer experience, internal production, and broader business objectives.
Inefficiencies not only waste time but also incur significant costs. Implementing a process improvement strategy using an established methodology ensures continuous identification and correction of such issues, leading to more efficient resource use and less waste.
This can lead to considerable savings by reducing the need for unplanned overtime and expensive shipping options.
Moreover, these methodologies improve product quality by incorporating thorough testing phases, ensuring that only products meeting all performance and security criteria proceed to production.
This attention to quality reduces the likelihood of costly recalls or customer dissatisfaction. Process improvement can also uncover opportunities for automation, giving employees time for more strategic tasks and boosting overall productivity.
Finally, staying engaged with process improvement methodologies positions a business to quickly adapt to rapid technological advances, evolving industry trends, and competitive shifts, maintaining its relevance and competitiveness in a fast-paced market.
18 Types of Process Improvement Methodologies
Process improvement methodologies differ in their objectives, durations, and levels of complexity.
Below are eighteen process improvement strategies that could suit your organization:
- PDCA Cycle
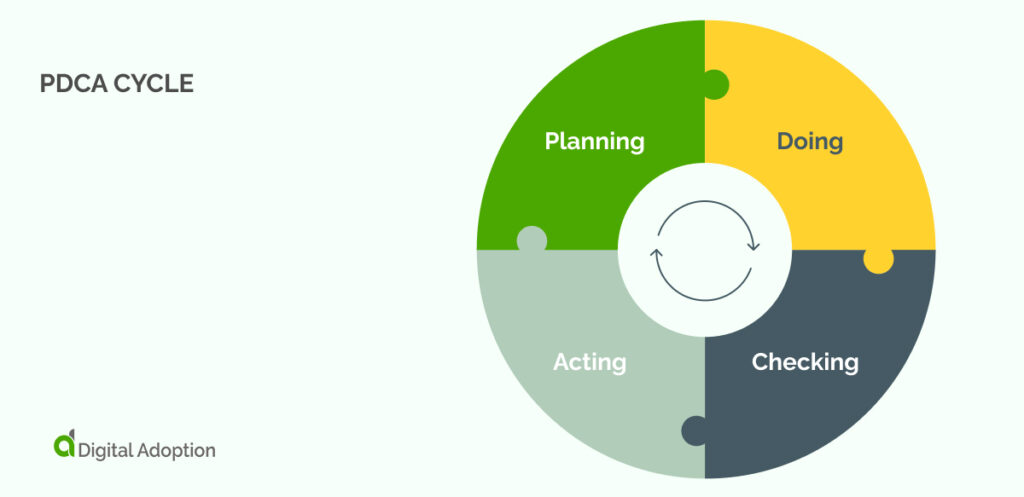
The PDCA cycle methodology was initially developed by Walter Shewhart, who incorporated the scientific method into his efforts in economic quality control. Designed for interactive problem-solving and process improvement, the methodology was later refined by W. Edwards Deming, who also applied it to process improvement and quality control.
The four fundamental steps of the PDCA cycle are planning, doing, checking, and acting. During the planning phase, a business identifies the problem it aims to solve and devises a solution. The next stage involves testing and implementing the plan on a small scale.
After completing the initial two steps, the process progresses to the checking and acting phases. These include evaluating the outcomes of the implementation phase and deciding whether to expand the changes on a broader scale.
The core principle of the PDCA cycle is to pilot improvements to business processes in a small, manageable environment and, if successful, extend those improvements across the company’s processes and workflows.
- Kaizen (Continuous Improvement)
Kaizen is a process improvement methodology emphasizing continuous improvement through a bottom-up strategy engaging the entire company. It aims to foster a company culture where employees across all levels are encouraged to identify, propose, and execute process improvements.
This approach focuses on engaging plant floor employees in manufacturing settings to play a significant role in process improvement efforts.
The practice of Kaizen revolves around so-called Kaizen events, which are the actionable steps toward enhancing processes. These events draw employee participation throughout the organization and encompass several key activities. Initially, it involves setting clear business or project objectives.
Following this, the current processes are reviewed to identify potential areas for improvement. Necessary modifications are then implemented.
After implementation, these changes are reviewed and adjusted to ensure they meet the intended goals. Finally, the outcomes are documented and reported, closing the loop on the improvement cycle and setting the stage for further enhancements.
- Theory of Constraints
This methodology emphasizes the rapid elimination of process constraints or bottlenecks.
It involves a sequence of steps starting with identifying the constraint, followed by systematic improvements to alleviate the bottleneck until it no longer hinders the process.
Created by Eliyahu M. Goldratt and introduced in the 1984 publication, ‘The Goal: A Process of Ongoing Improvement,’ the theory of constraints (TOC) is a management philosophy centered on achieving organizational goals by focusing on and addressing system constraints.
These constraints are factors that limit performance, and according to the theory, at least one such constraint is always present.
Goldratt’s approach shifts the focus from individual components and processes to optimizing the constraint. An organization can enhance profitability and effectively achieve its objectives by pinpointing and improving the element directly impeding progress.
Recognizing that organizations are complex systems comprising interconnected departments and individuals with numerous dependencies is crucial.
Actions in one area can have corresponding effects throughout the organization. Instead of resolving isolated or short-term issues among teams, the theory of constraints advocates for a broader perspective. This involves identifying a single leverage point within the system and addressing it to foster overall improvement.
Applying the theory of constraints unfolds through five pivotal steps, starting with identifying the current bottleneck. This is followed by exploiting the constraint, which involves dissecting the bottleneck to find immediate improvement opportunities.
Subsequently, the focus shifts to subordinating other processes to the constraint’s needs, ensuring the entire system is aligned to support its resolution.
The next step is to elevate the constraint’s capacity, enhancing the bottleneck’s performance. The final step acknowledges that solving one constraint often reveals another, necessitating a return to the first step to identify and address the next constraint, thereby preventing inertia and fostering continuous improvement.
- Total Quality Management (TQM)
This process improvement methodology is a continuous effort to minimize errors in manufacturing, enhance supply chain management, improve customer experiences, and ensure employees are well-trained.
Rooted in the early 20th century with Walter A. Shewhart’s work, TQM evolved through contributions from Joseph M. Juran and W. Edwards Deming, emphasizing quality control and systemic improvement in manufacturing.
Total quality management centers on customer satisfaction, continuous improvement, and employee engagement. It employs systematic methods, including process flowcharts and documented workflows, to ensure everyone involved in production understands their role.
This approach requires clear communication, strategic planning aligned with the organization’s vision, and effective use of data to guide decision-making and process evaluations.
TQM facilitates informed decision-making and efficiency improvements by integrating systems and encouraging collaboration across departments. Applicable across various industries, TQM aims for long-term systemic change, focusing on enhancing product quality, refining production processes, and ensuring all employees work towards common organizational goals.
- Kanban
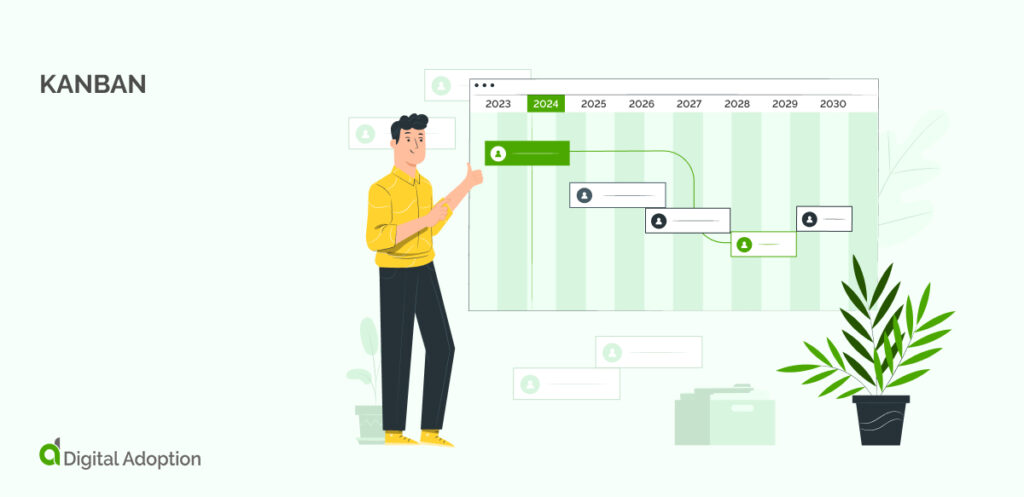
Kanban, a Japanese term meaning ‘visual sign,’ is widely used in organizations to manage and enhance workflow across systems, regardless of whether the official name is adopted.
This lean methodology is typically implemented using Kanban boards, cards, or flows that map out a project’s roadmap and the status of each component, offering a straightforward way to boost efficiency.
Commonly utilized in product management and development, Kanban can benefit any organization looking to enhance process and workflow efficiency without altering team structures.
Implementing Kanban is relatively simple, with the critical aspect being the ongoing monitoring and adjustment of the project roadmap as necessary. As a project advances, each process stage reaches its milestones, which may encounter bottlenecks.
Should bottlenecks arise, conducting a root cause analysis helps identify and address the underlying issues by eliminating them or preventing them from hindering the workflow. This focus on continuous improvement and efficiency makes Kanban an accessible and effective method for optimizing organizational operations.
- Six Sigma
Originating in 1986 at Motorola, Six Sigma is a methodology aimed at process improvement by identifying and eliminating defects or inconsistencies to ensure the delivery of flawless products or services.
Its core objective is to enable organizations to quantify process deviations and defects, improving the service and quality of products offered to their customers.
The methodology operates through a five-phase process improvement cycle, which consists of defining, measuring, analyzing, improving, and controlling (DMAIC).
The DMADV framework is also tailored to create new products, services, or processes rather than refining existing ones. This sequence—Define, Measure, Analyze, Design, Verify—proves particularly beneficial for launching new initiatives, relying heavily on data for early success indicators and in-depth analysis.
Six Sigma sets itself apart by its reliance on statistical data for decision-making, emphasizing the importance of the Define, Measure, and Analyze stages to pinpoint necessary enhancements and detail them through precise data metrics.
Following the identification of required improvements, the Improve and Control phases tackle the root causes of identified issues, subsequently managing the enhanced process to mitigate any further defects or variances.
- Lean Manufacturing
The Lean methodology focuses on cost reduction by eliminating process waste. Although commonly associated with manufacturing, its principles are universally applicable across various organizations and processes.
This approach involves scrutinizing a process’s value stream, which encompasses value-added activities (those actions a customer would willingly pay for) and non-value-added activities, which either develop a concept or fulfill an order.
In Lean thinking, any activity that does not add value or is not mandated by policy or regulation is considered waste.
This includes unnecessary product transportation, excess inventory beyond what is needed for current orders, unnecessary movement of people or equipment, and delays or interruptions in production.
Then, it also consists of producing more materials than demand, which requires extra work due to redundancies or suboptimal design, efforts related to identifying and rectifying defects, and the underuse of employees’ skills and knowledge.
Process engineers pinpoint these wasteful aspects to enhance product value. Lean methodology is anchored in five key principles. The first and second are understanding what the customer values and mapping out all steps, materials, and resources required to deliver a product or service.
Next, the focus is on removing barriers to ensure smooth workflow, creating a demand-driven system to minimize waste, and embracing continuous process evaluation and adjustment to achieve an ideal, waste-free operation.
- Business Process Management (BPM)
Business process management (BPM) is a complete approach covering everything from process modeling to automation, aiming for efficiency by identifying and resolving workflow bottlenecks. This includes automating repetitive tasks and eliminating redundant ones.
While some methodologies target physical manufacturing, BPM is particularly suitable for software companies because it emphasizes automated workflows. Continuous process reengineering allows for streamlining workflows, enhancing efficiency, and reducing costs.
Incorporating Six Sigma and Lean methodologies elements, BPM involves advanced analytics, activity monitoring, and decision management to coordinate people, systems, information, and materials toward achieving desired business outcomes. This approach has been instrumental in accelerating digital transformation efforts.
A successful BPM initiative begins with defining workflow stages to spot improvement areas and track progress metrics. Understanding the BPM lifecycle, comprising process design, modeling, execution, monitoring, and optimization, is crucial.
In the design phase, teams outline process milestones, identify tasks, assign task owners, and set clear definitions for optimization areas and performance metrics.
Modeling involves creating a detailed visual process representation, often facilitated by BPM software. Execution includes testing the BPM system with a small group before wider implementation, while monitoring involves tracking efficiency improvements and identifying further bottlenecks.
The final step, optimization, involves refining the process to enhance business activities. Effective BPM projects require meticulous planning and open communication, offering significant benefits upon successful activity improvements.
- People, Process, and Technology Framework (PPT)
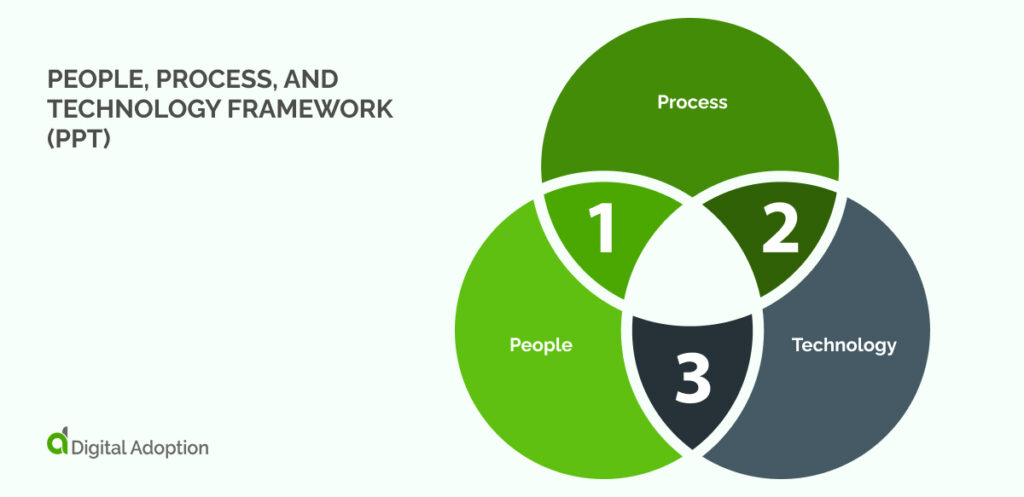
People, processes, and technology are indispensable components for organizational transformation and management, each pivotal in achieving organizational efficiency. It’s essential to balance these elements and foster strong relationships to ensure harmony within an organization.
The methodology known as people, process, and technology (PPT) emphasizes the importance of this balance, advocating for a systematic approach where people use processes and technology to enhance their work and streamline operations.
This framework, particularly relevant in decisions related to acquiring or implementing new technologies, is widely applied within information technology management.
The origins of the PPT framework trace back to the early 1960s, developed by business management expert Harold Leavitt, who introduced a model for organizational change. This model set the stage for a systematic approach to assess the interplay between different organizational factors.
By the 1990s, security technologist Bruce Schneier further highlighted the significance of integrating people, processes, and technology, emphasizing the interconnected evolution of these components and the holistic impact of change across an organization.
This perspective challenges the conventional focus on technology and processes at the expense of considering the human element, advocating for a more inclusive approach to decision-making and continuous improvement.
Successful change initiatives require engaging people beyond the management circle and acknowledging the importance of their contributions to sustainability and long-term success.
It’s crucial to identify the organization’s primary challenges, whether they relate to speed, efficiency, or innovation, and address these by examining the interactions between people, processes, and technology.
This may involve leveraging existing technology more effectively, automating processes where possible, scaling human and process interactions efficiently, and fostering innovation at the intersection of human creativity and technological capabilities.
Moreover, critically examining the organization’s culture, particularly how decisions and changes are communicated, is vital for successfully implementing change. Training and development are important in ensuring individuals are equipped for success, emphasizing the need for clear communication and a supportive environment.
By adopting a comprehensive view that integrates people, processes, and technology, organizations can navigate the complexities of transformation, ensuring a balanced approach that addresses immediate challenges while paving the way for sustainable growth and innovation.
- 5 Whys
The 5 Whys is a straightforward yet effective root cause analysis tool designed to drill down to the root cause of problems by exploring the factors contributing to an outcome. This method allows for a transition from identifying contributing factors to uncovering the root causes that lead to an issue.
For instance, if there have been more complaints in the last few months about a product that normally receives positive feedback, the goal would be to understand why the complaint occurred and what could have been done differently.
If productivity drops and more people leave the company, the 5 Whys method suggests digging deeper to find out why employees are leaving and if it’s linked to the earlier complaint. This method is also valuable for reframing thinking and reducing biases.
For effective implementation, especially with complex issues, it’s advisable to convene a knowledgeable team. Organizing a time-bound session focused on a specific problem facilitates a structured exploration of the issue using the 5 Whys.
Pre-defining the problem and bringing people together allows for a comprehensive examination from multiple perspectives. Having a facilitator to guide the session and document ideas can significantly enhance the workflow, ensuring the process is thorough and efficient.
- Fishbone diagram (cause and effect analysis)
The cause and effect analysis methodology, also known as the Ishikawa or Fishbone diagram, serves as a root cause analysis tool to identify potential causes of an event.
Professor Kaoru Ishikawa introduced this methodology in the 1960s as a tool for quality control. Primarily utilized in product design and quality defect prevention, the fishbone diagram aims to uncover factors that could lead to a particular effect.
This methodology finds application across various industries due to its effectiveness in identifying and analyzing all possible causes for a problem or effect. It is precious during team problem-solving brainstorming sessions as it facilitates a structured approach to identifying issues.
Additionally, the fishbone diagram aids in documenting information related to the issues under analysis, enhancing its utility. Its ease of use is evident as it enables teams to identify and analyze the causes of a problem comprehensively within a single brainstorming session.
- Gemba Walks
The Gemba walk represents a critical element within the continuous improvement toolkit, characterized by its observational approach that allows managers and leaders to engage closely with the operational aspects of their organization.
The term ‘Gemba,’ derived from Japanese, translates to ‘the place to be’ and signifies the locations within an organization where value creation occurs.
Thus, applying Gemba walks is particularly emphasized in areas integral to the operational workflow, such as manufacturing floors, hospital operating rooms, and construction sites.
Contrary to its seemingly straightforward nature, conducting a Gemba walk is far from simple. It demands leaders with the insight to observe and understand nuances from a distance, coupled with meticulous planning.
A well-thought-out plan and a definitive objective for effective implementation must guide these walks.
Leaders embarking on a Gemba walk should first clarify their goals, whether it is to gather insights, identify areas for improvement, assess processes, or evaluate communication channels.
During Gemba walks, leaders must refrain from disrupting operations or directly suggesting immediate corrections. Instead, their focus should be on observing and seeking to comprehend the actions and decisions of team members.
Developing a structured itinerary for the walk can prove beneficial, allowing leaders to systematically explore various departments such as sales, shipping, and production.
Additionally, employing a checklist, particularly in the initial stages, can aid leaders in maintaining focus and ensuring a comprehensive understanding of each area under review.
- SIPOC analysis
The Suppliers, Inputs, Process, Outputs, and Customers (SIPOC) framework offers a high-level visualization of processes, making it an effective tool for process improvement.
Designed to provide a broad overview rather than delve into detailed intricacies, SIPOC is particularly useful for comparing multiple processes at once and quickly aligning team members with project objectives.
This methodology is commonly applied at the beginning of projects to gain an overarching perspective, clarify the various components of a process, and communicate the project’s scope to stakeholders.
It is most beneficial for businesses in the initial phases of process mapping, teams seeking clarity on roles, responsibilities, and deliverables, and for mapping complex processes across different departments or teams.
- Just-In-Time
The just-in-time (JIT) inventory system, also known as the Toyota Production System (TPS) after its adoption by Toyota in the 1970s, is a management strategy designed to streamline production and reduce waste.
By aligning raw-material orders directly with production schedules, companies can increase efficiency, reducing inventory costs by ordering goods only as needed for production.
This approach demands accurate demand forecasting and is complemented by the Kanban scheduling system to prevent overcapacity in the production process. The effectiveness of JIT hinges on consistent production, high-quality outputs, the reliability of machinery, and dependable suppliers.
Various terms such as short-cycle manufacturing, coined by Motorola, and continuous-flow manufacturing, used by IBM, are synonymous with JIT, highlighting its wide applicability.
From small businesses to large corporations, industries ranging from retail and restaurants to on-demand publishing, tech, and automobile manufacturing have seen significant benefits from implementing just-in-time inventory, including improved cash flow and reduced operational capital.
- Agile
Agile methodology emphasizes an iterative approach to project management and process improvement, favoring incremental steps over rigid deadlines. This flexible system, characterized by ‘scrum’ and ‘sprint’ meetings, facilitates the incorporation of team feedback and the identification of both problems and successes.
It allows for speed, budget, and quality adjustments, maintaining flexibility in the project scope to accommodate changes better.
Implementing process improvements in an agile framework involves creating a backlog of changes, identifying processes needing enhancement, diagnosing current inefficiencies, establishing priorities for tackling challenges, acting on brainstormed solutions through pilot changes, and learning from the outcomes to inform further improvements.
The enhancement process is structured into short, incremental work periods known as sprints, through which workflow improvements are progressively developed and implemented.
These include creating prototypes to test changes on a small scale, piloting them to assess their impact, deploying them on a larger scale, and evaluating their performance. Each sprint is allocated a specific timeframe, allowing for the reassessment of priorities upon completion, ensuring continuous and adaptive improvement.
- Value Stream Mapping
Value stream mapping is a lean manufacturing methodology used for analyzing, designing, and managing the processes responsible for bringing a product from conception to the customer.
It employs a set of standardized symbols to represent different work and information flows, categorizing activities into those that add value and those that do not, from the customer’s perspective. The goal is to identify and eliminate non-value-adding activities.
This technique is beneficial in processes with repeatable steps and multiple handoffs, such as in manufacturing, where handoffs typically involve the physical transfer of items across various stages. For instance, if an issue in vehicle assembly leads to a bottleneck, workers can easily spot the problem area, halt production, and address the issue to restore flow.
Beyond manufacturing, value stream mapping is increasingly applied in knowledge work fields, enhancing team communication and collaboration.
It highlights inefficiencies often found in the wait times or handoffs between team members, which can significantly hamper productivity and quality. Value stream mapping facilitates a more efficient production process by pinpointing these waste areas.
The approach is adaptable to both product and customer delivery flows. In the context of product flow, it aims to refine the steps necessary for efficient product delivery and completion. For customer flow, the focus shifts to optimizing the steps that fulfill end-user requests and meet their expectations, ensuring a smoother delivery of services or products.
- Process Mapping
Process mapping is a technique used to visualize the workflow within a company, aimed at planning and enhancing process improvement from beginning to end.
This can be executed through various forms, such as process flowcharts, functional flowcharts, or process models. By employing tools for process mapping, organizations can develop maps tailored to specific roles or objectives, enabling a detailed analysis of activities to boost productivity.
- 5S
The 5S model, integral to lean and Kaizen methodologies, facilitates continuous and swift improvements by focusing on five foundational principles, starting with the letter ‘S,’ to enhance employee efficiency and effectiveness.
These principles involve sorting, keeping commonly used items nearby, and straightening and organizing the workspace to access items quickly within 30 seconds, avoiding task delays.
Next, it also features Shine, maintaining equipment and resources in a ready-to-use condition; Standardize, ensuring tasks and activities are performed uniformly while encouraging the sharing of improvement ideas; and Sustain, maintaining a safe, efficient, and effective workplace.
Implementing the 5S methodology not only enhances safety and reduces costs but also boosts team efficiency by eliminating waste from manufacturing processes and bringing consistency and standardization to process improvements.
What’s next for process improvement methodologies?
Process improvement methodologies focus on identifying, analyzing, and resolving bottlenecks, challenges, and opportunities within business operations. They intersect significantly with project management, business strategy, and customer experience initiatives.
Implementing process improvement methodologies can significantly illuminate inefficiencies in current operations and offer strategies to enhance or streamline processes. While these techniques alone won’t transform your organization into a model of perpetual enhancement overnight, they are instrumental in setting you on the right path.
It’s crucial to acknowledge that no universal solution fits every scenario. However, tailoring a combination of these methodologies to your specific requirements can yield substantial benefits.
For businesses engaged in manufacturing or those prioritizing a data-centric approach to refining processes, methodologies like Six Sigma, PDCA, or Lean Six Sigma could serve as excellent starting points.
Kanban, the 5 Whys, or Value Stream Mapping might be the ideal choice for organizations aiming to maintain a clear overview of ongoing process enhancements.
Alternatively, business value stream mapping could prove invaluable for those seeking to dissect processes meticulously to optimize product quality and customer satisfaction.
The essence of effectively implementing these methodologies lies in experimentation; by trying various approaches, you can discern which ones align best with your team’s preferences, which are the most enjoyable to employ, and which ultimately drive the most impactful improvements.